What is Water Glass Casting
Water glass casting is also called sodium silicate casting. Its casting process is very similar to investment casting (that is the lost wax investment casting method). It is a technology that uses water glass as the binder for the shell to cast. The process provides a far superior surface finish and dimensional precision to that achieved through sand casting. And more complex shapes can be achieved.
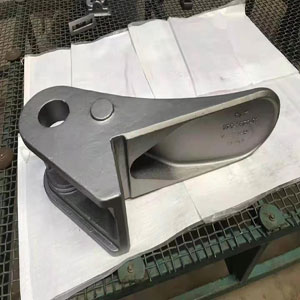

It is particularly suited to larger castings and is cheaper to produce. The raw materials are mainly steel and iron.
The Water glass casting technology is from Russia. Now it is one of the most common investments casting processes in China. About 75% of foundries focus their business on water glass casting. the rest are silica sol casting factories.
Benefits of water glass casting
JC Casting is a water glass casting manufacturer and supplier. We have a wealth of experience in manufacturing water glass components.
To summarise, the water glass process Benefits:
- Superior surface finish than sand casting.
- Greater dimensional precision than sand casting.
- Achieve more complex parts.
- Suited to larger parts than the traditional investment casting method.
- Cheaper than investment casting.
- Short Lead time than investment casting.
- Greater choice of metals.
- Environmental advantages. (the wax is completely recyclable.)
Water Glass Investment Casting Process
The difference between the lost wax method and water glass casting is simply the way the wax is removed from the ceramic mold:
Investment casting uses high-temperature autoclaves to melt the wax, whereas:-
In Water glass casting the molds are submerged in hot water to remove the wax. The wax is then melted away from the molds and it floats on the surface of the water. This then allows for it to be skimmed off and reused for wax-making purposes.
Obviously, this also provides environmental advantages and the wax is completely recyclable.
Step 1:Wax Injection
For each casting desired, the melted wax is injected into a mold to produce a wax pattern of the casting. The wax molds are made of Aluminum and sized to account for shrinkage in the wax and metal that are being used. Wax tooling ranges from simple two-piece dies to multi-cavity automated dies and complex dies featuring water-soluble or ceramic cores.
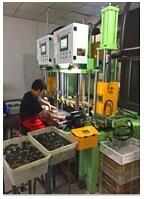
Step 2: Wax Assembly
Once the wax patterns have cooled and settled to a stable size and shape. They will be mounted onto a sprue or tree. The sprue which is also made of wax contains all of the necessary gates, runners, and supports to adequately feed the part during the casting process
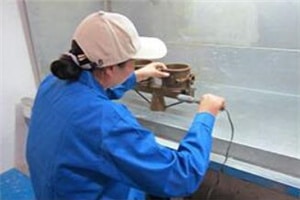
Step 3: Shell making
The wax sprue is now “invested” in ceramics. This creates the mold for the metal to be poured into. The ceramic consists of two parts. The surface is a liquid slurry covered with dry sand. Each sprue is covered in many layers of slurry and sand. Until the ceramic shell is thick enough to hold up during the casting process. The shell building time usually takes 1 day. And also need 2 days to almost 1 week for the shells to fully dry.
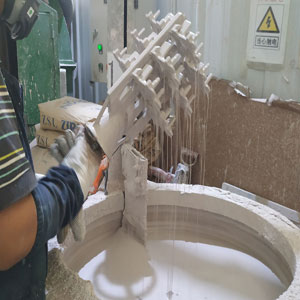
Step 4: Dewax
Once the shell has fully dried, The shells can be fired to remove any remaining wax residue and cure the ceramic shell. After the shells have been fired, they are ready for the casting pouring
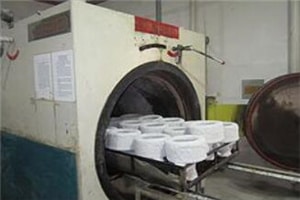
Step 5: Pouring
Before casting, The processed shells are placed back in the oven to be pre-heated. When the shells are at the proper temperature and the molten metal has been prepared and qualified. The shells are removed from the oven and the metal is poured into the shells.
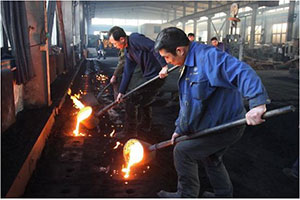
Step 6: Finishing
The shell is hammered, media blasted, vibrated, waterjet, or chemically dissolved (sometimes with liquid nitrogen) to get the finished casting. The sprue is cut off and recycled. The casting may then be cleaned up to remove signs of the casting process. Usually by grinding.
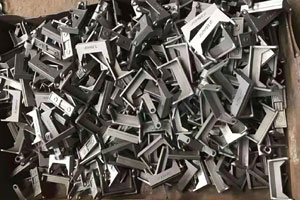
JC Casting Water Glass Casting Parameters
Applicable Material | Cast steel, cast iron, stainless steel, nodular cast iron, high chromium iron, high manganese steel,alloy steel ,Non-ferrous steel alloy,Heat-resistant steel |
Material Standard | GB, ASTM, AISI, DIN, BS, JIS, NF, EN, AS, ARR |
Weight | 0.02kg-50kg |
Tolerance | CT 5~7 |
Surface Roughness | Ra 6.3 |
Annual Output | 1200T |
Application | Auto, motorcycle, valve, marine, machine tools, hardware, railway, gear, impeller, pump, reducer, motor, mining machinery, engineering machinery, transmission machinery, forestry machinery, communal facility, etc. |
Drawings software | Pro/E, Auto CAD, Solidwork, CAXA UG, CAD/CAM/CAE. |
Machining | Turning, milling, drilling, grinding, threading, NC, etc. |
Finishing | Sandblasting, polishing, plating, acid treatment, anodizing, painting, etc. |
Download the document: What is Water Glass Casting?
Why do we choose Water Glass Casting?
Water glass casting is seldom in other countries. But in China it is more, about 75% of foundries focus their business on water glass casting. So what is water glass casting?
The water glass casting process was introduced to China in the mid of 1950s. It is different from the ethyl silicate binder investment casting process. Due to the advantages of material cost and short production cycle. The water glass casting was quickly applied in civil machinery manufacturing. With the fast development of the water glass casting process in China for more than 70 years. Its production scale and application field has become the mainstream investment casting industry.
By adding 0.5% penetrant, the surface quality of water glass casting is greatly improved. The surface finish can even be comparable to the silica sol casting technology. It can avoid defects caused by traditional shell-making technology. At the same time, the working environment is improved obviously.
Besides, the process parameters and operation requirements are not so complicated and strict. The general workers are available to operate shortly. This reduced the loss of skilled workers. And the new workers are also workable, which stabilized the normal production efficiency of the factory. About costs, shell-making material cost is not added compared with the traditional hardening process. This process decreased the weld repair processing significantly. Improving the product rate shortens. And thus to reduce the production cost and production efficiency.
Water glass casting Applications
Water glass cast components are mainly used for heavier or stronger, more complex shapes products. These applications are in the field of trailers, agricultural machinery, and the offshore industry. The process provides a far superior surface finish and dimensional precision than sand casting. It also allows for more complex shapes to be achieved. Besides steel, it is possible to cast alternative materials. Such as regular iron using this method.
Contact us here for more information about JC Casting, obtain a quote, or to discuss your water glass project requirements in more detail. Alternatively, please get in touch using the details below.
Water glass casting inquiry
Contact:
Tel: +86 181 05467890 Email: [email protected]