Casting is an important process in manufacturing. Countless industries rely on products made out of casting. A casting forms by pouring melted material into a mold. Once it has solidified, it becomes a component that can come in different shapes and forms. The molder depends on the type of component needed. Such as alloy casting!
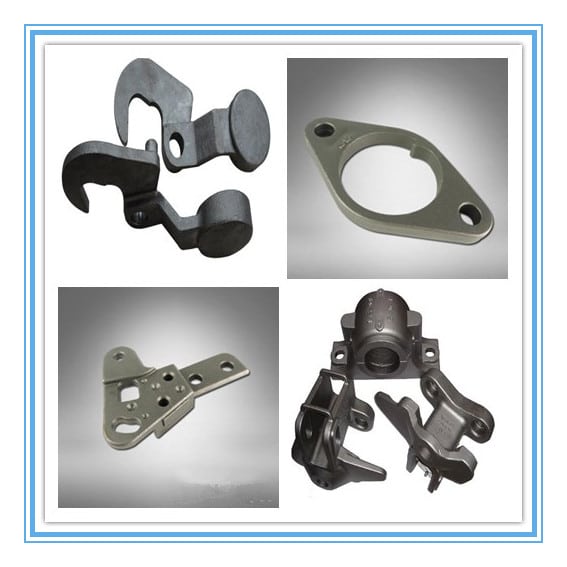
What is alloy casting?
With casting, the most popular material used is iron, steel. But alloys are also becoming more known to people. Alloys are different metals combined with other substances. This results in stronger, lighter, or more durable castings.
Alloy casting is melting alloys and following the procedure of traditional casting. This is also used by many industries. They rely on the products produced from alloy casting. Alloy casting has a lot of features to offer. These make it interesting and appealing to industries and manufacturers.
Alloy Casting Features
Alloy castings have features which preferable by many manufacturers and industries. These include:
- Fluidity
Alloys, when melted can flow well. This makes it easy to work with. And it also helps in making the process easier and faster to finish. Alloys can be easy to melt especially when it uses a high melting metal.
- Machinability
Its machinability features relate to its fluidity. Alloy casting is easy to machine and form. This helps in producing the required components. Machinability does not end when the casting has solidified. There are still a lot of procedures performed to create the required component. This is when alloy castings are most useful as it is a high machinability feature.
- Corrosion Resistant
Alloy casting is corrosion-resistant if they choose the right substances. In this case, one should choose materials with high corrosion strength. It is easy to create corrosion-resistant alloy casting. You have to combine a rust-proof metal with the right substances.
- Strength
Alloy castings are strong and durable. This happens when the metal chosen has high strength. Combining the metal with different substances can result in a stronger casting. The proper choice of metal can dictate the strength of the product will become.
The features that alloy castings have may rely on the metal and substances used. To get the desired feature for the component, you should choose the right metal to use.
Alloy Casting Types
Zinc Alloys
Zinc alloys have low melting points. It is a type of alloy casting that easy to machine and has high flexibility. Its strength may not be suitable for high-temperature and compression environments.
- Common Products
- Jewelries
- Electrical equipment
- Batteries
- Common Applications
- Automotive
- Medical
- Construction
- Marine
Tin Alloys
Tin alloys are strong and durable. This is often used in coating and surfaces of different products and components made of metal. But it is also used in industrial equipment and tools. Tin alloys have low melting points.
- Common Products
- Tin Cans
- Tin Coated Steel
- Superconducting Magnets
- Common Applications
- Useful in making organ pipes
- Used in making bearing materials
- Used as hot-dip coating
Copper Alloys
Copper alloys can be sturdy but have difficulties keeping up with high temperatures. It is often used to create products that need strong surfaces. It is workable and with good machinability.
- Common Products
- Bells
- Trumpets
- Gongs
- Radiator Cores
- Common Applications
- It is useful in making musical instruments
- It can make technical instruments
- It is useful in making elbow fittings and water pressure regulators
Aluminum Alloys
Aluminum alloys have better strength as compared to other alloy casting types. It is also among the more popular in the market. Using aluminum alloys speeds up the process of manufacturing. It is because of its fluidity and machinability properties.
- Common Products
- Food packaging trays
- Aluminum frames
- Can lids
- Common Applications
- Used in structural and automotive equipment and parts
- Used in making marine equipment and machines
- Useful in making kitchen and baking tools and utensils
- Used in making electrical equipment
- Useful in the plane industry
Lead Alloys
Lead alloys are popular to be corrosion-resistant materials. The performance of lead alloys may be inferior as compared to other alloy casting types. But, there are still lots of products that use lead alloys.
- Common Products
- Automotive batteries
- Cans
- Automobile gasoline tanks
- Common Applications
- It is most useful in the automotive industry
- It is useful in roofing and packaging
- It is useful in the chemical industry
Alloy casting provides a lot of purposes for many industries. It is as useful as the other types of casting. This is also useful in creating needed components in different designs, and forms.
Metal Materials Used in Alloy Casting
As mentioned, alloy casting works by combining a metal with other substances. With this, the use of different metal materials can produce an alloy casting.
Aluminum
In using aluminum to create alloy casting, one can get many properties. Among these are corrosion resistance, machinability, and weldability.
Carbon Steel
This helps in making products that are strong and durable. But its corrosion resistance level is low.
Nickel
Alloy castings using nickel can offer a lot of benefits. Among these are high oxidation resistance, machinability, and weldability.
Cobalt
Products that use cobalt in alloy casting can have good resistance to corrosion.
Stainless Steel
When using stainless steel to cast alloy, the products produced are strong. They are also corrosion-resistant and oxidation-proof.
Conclusion
Alloy casting is an efficient casting type that can create different products. Most industries rely on alloy casting. It is because it can create components that can help keep the industry working and moving. There are different metals to choose from when working on alloy casting. The choice of metal should depend on the type of product needed. The manufacturer also needs to determine the properties needed by the products. This way, they can choose and use the best metal for casting alloys. There are experts in this matter. They can provide the right type of alloy casting for the product or component needed.