What is Heat Treatment?
Metal heat treatment is an important process in mechanical manufacturing. It refers to a metal thermal processing to get the desired structure and properties via heating, warming, cooling method. It is an essential part of the manufacturing process.
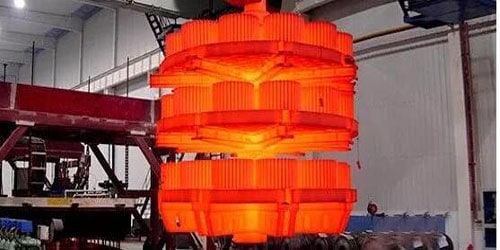
Compared with other manufacturing techniques, heat treatment generally does not change the shape of the workpiece and the overall chemical composition. Instead, it improves the performance of the workpiece by changing the microstructure inside the workpiece. Or changing the chemical composition of the surface of the workpiece. It is characterized by the improved internal quality of the workpiece. It is not visible to the naked eye. The essence of heat treatment is the physical change of the object. It is a process that improves its service performance, and service life by strictly controlling the heating and cooling process of the metal material.
What is the purpose of heat treatment?
The purpose of heat treatment: to change the inner structure of the shape of the material and improve its performance. Including process performance, mechanical property, or combination of mechanical. To use the potential of the material can be fully utilized to improve the intrinsic quality of the part.
What products or materials need heat treatment?
Materials: More than 80% of heat-treated metals are different grades of steel. The metals that can be heat treated including cast iron, stainless steel, and different grades of tool steel.
10#、20#、20G、20ANTI-HCI, 16Mn、16MnR, 09MnNiD, 15CrMo、15CrMoG.
Products: Knives, molds, rolling bearings, wear parts, springs, clockwork, connecting rod crankshafts, gears, important screws, steel plates, pipes, engine blocks, pistons, fasteners.
Heat Treatment Process
The heat treatment process generally includes three processes of heating, soaking and cooling. Sometimes there are only two processes of heating and cooling. These processes are connected to each other and cannot be interrupted.
1. Heating Process
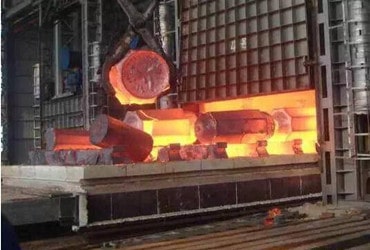
When the metal is heated, the workpiece is exposed to the air, and oxidation and decarburization. That is to say, the carbon content on the surface of the steel part often occurs. It has a detrimental effect on the surface properties of the parts after the heat treatment. Thus the metal should normally be heated in a controlled or protective atmosphere, in molten salt and a vacuum. Protective heating can also be carried out by coating or packaging methods.
You get even heating by heating slowly. If you heat the metal unevenly, one section may expand faster than another, resulting in a distorted or cracked section of the metal.
You choose the heating rate according to the following factors:
- The metal heat conductivity. Metals with high heat conductivity heat faster than those with low conductivity.
- The metal condition. The hardened or stressed Tools and parts should be heated slower than tools and parts that haven’t.
- The metal size and cross-section. Larger parts heating speed is slower than small parts. To allow the inside temperature to be close to the surface temperature. Otherwise, there is a risk of cracking or excessive warping.
Soaking Process
In the soaking stage, the purpose is to keep the metal at the appropriate temperature until the desired internal structure takes shape. The soaking period is the time to keep the metal at the appropriate temperature. The length of time is determined by the chemical analysis and mass of the metal. For uneven cross-sections, you can use the largest section to calculate the soaking time.
Generally, It can not bring the metal temperature from room temperature to the soaking temperature directly. Rather, the metal heating is slowly to just below the temperature where the structure will change. Then keep it until the temperature is consistent throughout the metal.
After preheating, the heating temperature can be fast to the final temperature needed.
Cooling Process
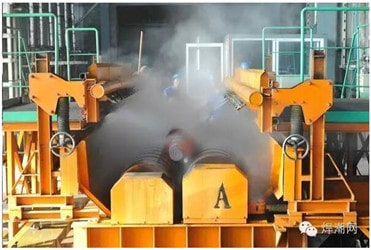
Cooling is also an indispensable step in the heat treatment process. The cooling method varies from process to process, mainly to control the cooling rate. The rate of cooling depends on the metal itself and the medium for cooling. For the cooling process, there are different ways to do this depending on the metal types. It might need a cooling medium, a gas, liquid, solid, or a combination.
For example, Quenching can rapidly cool metal in air, oil, water, brine, or another medium.
But quenching is associated with hardening. Most metals that are hardened are cooled rapidly with quenching. but quenching is not always true for hardening. For example, Water quenching is used to anneal copper. But other metals are hardened with slow cooling.
So the rate and medium of cooling chosen must fit the metal.
Main Heat Treatment Methods
Metal heat treatment processes can be roughly divided into three categories: Integral heat treatment, surface heat treatment and chemical heat treatment. Depending on the heating medium, heating temperature and cooling method. Each category can be divided into several different heat treatment processes. The same metal uses different heat treatment processes to get different microstructures and thus different properties. Steel is the most widely used metal in the industry. Its microstructure is also the most complex. So, there are many kinds of steel heat treatment processes.
The most common heat treatment methods include:
- annealing
- normalizing
- quenching
- tempering
Annealing
Annealing involves heating the steel to a suitable temperature. Holding it at that temperature for some time. Then cooling it slowly. There are different methods of cooling.
The main purpose of Annealing is to reduce the hardness of a material.
Besides this, it is also used –
-To relieve the internal stress of a material
-To restore ductility to perform the further operation on the material
-To induce softness
Normalizing
Heat the steel from 30℃ to 50℃ above its upper critical temperature. Hold it for about fifteen minutes, and then be allowed to cool down in still air.
The homogeneous structure provides a higher yield point, ultimate tensile strength, and impact strength with lower ductility to steel.
Main objective
-Refine grain, improve machinability, tensile strength, and structure of weld.
-Remove cold worked stress.
-Remove dislocations due to hot working.
Quenching
Quenching mainly involves the rapid cooling of a metal to adjust the mechanical properties of its original state. It heats the steel to 30 – 50° above the critical range. Then the steel is rapidly cooled through a cooling medium. The coolness from the quenching process is distributed throughout the thickness of the material.
Hardening increase the brittleness in the metal.
Tempering
Tempering is a heat-treatment process consisting of reheating the hardened steel to a temperature below 400℃, then cooling.
Tempering can reduce the hardness of a hardened alloy.
JC Casting is an investment casting foundry in China. We can cast most iron, steel, alloy materials for perfect casting. In our factory. We can offer different heat treatment methods for your products.If you have any casting that needs heat treatment. Call us today!