Automotive Investment Castings
Vehicle manufacturing is the most common use for casting in the automobile industry. JC Casting is a brand leader in automotive parts and investment casting parts. Auto castings and parts are essential to a vehicle’s function and reliability. We have been globally expanding its top-level automotive parts business.
At JC Foundry, we take great pride in manufacturing Stainless Steel Casting, Carbon Steel Casting, ductile castings and gray iron castings, Die Castings to meet client’s automotive requirements.

Our Expert design engineering combined with our advanced melting capabilities and finishing systems deliver high-quality gray iron and ductile iron castings that meet the most exacting OEM specifications. To save you production time and bring you the best possible cost.
Over the 22 years, we, as an auto castings manufacturer, have been manufacturing high-quality automotive castings for a range of purposes in the automotive market. We have a great of experience manufacturing castings for the automotive industry. Our automotive castings have used the castings of choice for many leading vehicle manufacturers. Especially exporting to USA Market and Japanese Markets.
Why use Auto Casting?
Casting is the most commonly used method of blank production. Different Casting methods can produce various types of auto castings with complex shapes.
Some parts require wear resistance, pressure, vibration, and low cost (such as pistons, piston rings, cylinder liners, cylinder blocks, etc.).
Some parts of automotive that are complex in shape and difficult to shape by other methods (such as cylinder heads, gearbox housings, and intake and exhaust manifolds) can only be produced by casting.
With the development of casting technology, the application range of castings continues to expand. Forgings commonly used in the past have been replaced by castings. Such as crankshafts, connecting rods and gears.
The main features of auto castings are thin walls, complex shapes, lightweight, good reliability, high dimensional accuracy, and large annual production volume. Such as cylinder block, transmission case, steering gear housing, rear axle housing, brake drum, various brackets, etc.
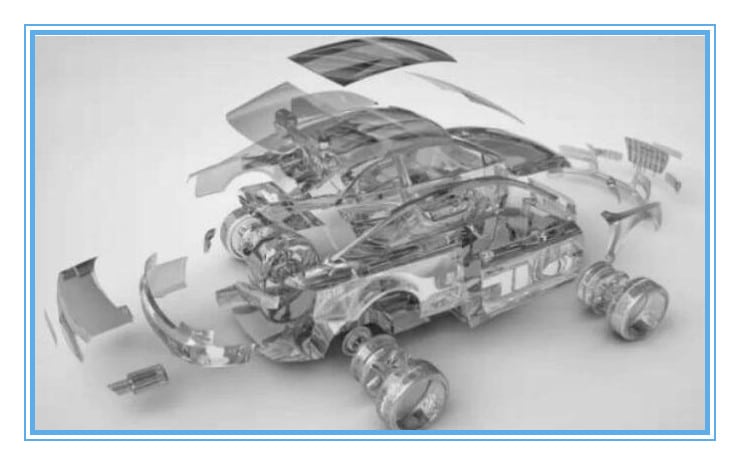
The main 6 Auto Castings Materials and Characteristics
1.Automobile gray iron castings:
A representative gray iron casting in a car is a cylinder block. Its development direction is thin walls and high strength. There are two main types of implementation.
One is the low-carbon process.
It is mainly to reduce the strength of cast iron by reducing the C and Si content of gray cast iron. The advantage is that it can be realized by changing the ingredients after the furnace. The reliability is high. Without or with little content of alloying elements. The cost is lower.
The pretreatment and operation requirements are relatively loose. The disadvantages are also obvious: low carbon equivalent and poor casting performance. It is easy to cause shrinkage (loose) waste and increase casting stress. The processing properties of the castings, the uniformity of the section are poor. And the thermal conductivity of the casting is affected.
The second is the high carbon equivalent and alloying process.
To maintain the C and Si content of gray cast iron at a higher level (wC>3.3%) and by adding alloying elements. Such as chromium, copper, etc., to improve the strength of cast iron. At present, the development of multi-microalloying is increasing.
The advantage is the alloying process is mature. The effect of the strength increase is obvious. The casting performance is good. The tendency to form shrinkage (loose) waste products is small. The processing and thermal conductivity of the castings are good. The disadvantage is that the alloying elements are added more. Casting costs are not only high but poor handling. So it can also affect the processability and leakage of castings. The pre-processing requirements are more stringent.
As the engine power increases, the performance requirements for gray cast iron are further improved. Some cylinders of engines have been manufactured by HT300 or even HT350. FAW Foundry has used HT300 to produce 6DL and Deutz engine blocks. At the same time, it also reserves the production technology of HT350. By optimizing the smelting process, materials and alloying process. The high performance and high-speed cutting of the cylinder material were successfully solved.
2. Ductile iron auto castings
Ductile iron is mainly used in automobiles. Such as crankshafts, camshafts, mid-rear axle shells, various brackets, and shells.
3. Vermicular iron castings
Vermicular graphite iron has been widely used in automotive castings. Such as automobile exhaust pipes and high horsepower engine cylinder heads. Medium and high-power engine cylinder heads are manufactured using vermicular graphite cast iron. One side. the weight of the cylinder head can be reduced by design. On the other side, the performance of the cylinder head improved can improve the power of the engine. The application of compacted graphite iron is mainly difficult to stabilize the control process.
4. Austempered ductile iron (ADI)
Austempered ductile iron has comprehensive mechanical properties with high strength, ductility, and toughness.
It is roughly divided into two categories, namely high strength type with the strength of 1200-1600 N/mm2 and elongation of 900-1200 N/mm2. 10% high toughness type.
Due to its excellent material properties, it has developed rapidly in developed countries of Europe and America. It has successfully applied ADI products in truck chassis, engines and car crankshafts.
In the European market, ADI is increasingly used in cars, accounting for 32% of the entire ADI market. In the US market, heavy-duty and light truck ADI components account for 51% of the entire ADI market
5. Special cast iron
With the improvement of engine performance, the heat resistance requirements of some castings, such as exhaust pipes, are getting higher and higher. So silicon molybdenum ductile iron, medium silicon molybdenum iron and high nickel ductile iron appeared.
6. Aluminum Zinc Alloy
This amazing metal provides strength, flexibility, and malleability that you cannot match with other materials. Aluminum and Zinc have a lowering melting point, allowing for less energy during production.
So if you have an inquiry about the automotive castings,we can confirm the casting materials types and technology.
Different Auto Casting For Automobile
Investment auto casting is able to produce an aesthetic appearance while providing the capabilities of creating unique shapes with a high durability tolerance. It carries high anti-corrosive properties, making it the ideal element for the automobile industry.
Here is a list of some of the parts that you can manufacture using this process:
- housing-auto-casting
- Investment Casting Auto Part
- die-casting-automotive-parts-castings
- Carbon-Steel-Auto-Casting
- EXHAUST SYSTEMS
- IMPELLER AND COMPRESSOR WHEELS
- CLUTCH COMPONENTS
- VOLUTES
- GEARBOX COMPONENTS
- DRIVESHAFT COMPONENTS
- VEHICLE BODY HARDWARE
- Chassis Parts
- Transmission Components
- Air-Conditioning Systems
- Engine Parts
- Power Steering Systems
- Brake Systems and Hardware
- Other Mechanical Parts
- And More…
JC Auto Castings Services:
1-Assembly analysis/casting integration:
We work closely with our automotive clients, to identify new approaches and opportunities to save. For instance, we saved one customer 60% in production costs by figuring out that two castings and one piece could be cast as a single piece. With our help, the company could recoup its costs in under two years.
2-Materials Anylasising:
We’re also capable of analyzing chemical and metallographic characteristics to identify materials and post-production techniques utilized. After this is determined, we consult with our clients to create an effective course of action to move to production.
3-3D Prototypes Design:
3D Prototypes Design is a physical prototype. Prototypes help test the efficiency of a manufacturing process and give an accurate preview of how a part will look, feel and handle. Oftentimes, the prototypes we produce are fully functional.The customer can feel it directly.
If you have a need for high quality auto investment castings, we can help you to fulfill your needs. For more information about your automotive industry components and producing. Welcome contact us, and our team will assist you happily .
JC foundry Auto Casting process
Auto Casting Methods
The 3 main casting method can be used in our foundry.
- 1–Investment Casing
- 2–Sand Casting
- 3–Die Casting
For more introduction about the casting method,you can view the article of 3 main casting method.
The CNC service
Turning,Milling,Drilling,Wire EDM,Grinding,Engraving,Tapping,Knurling,And other sub machining processes,Etc
Surface Treatment
Anodizing,Sandblasting,Painting,Powder coating,Plating,Silk Printing,Brushing,Polishing,Laser Engraving
QC Standard
For each auto castings, we request ourselves 0 defects,100% inspection before packing. with precision inspection equipments.