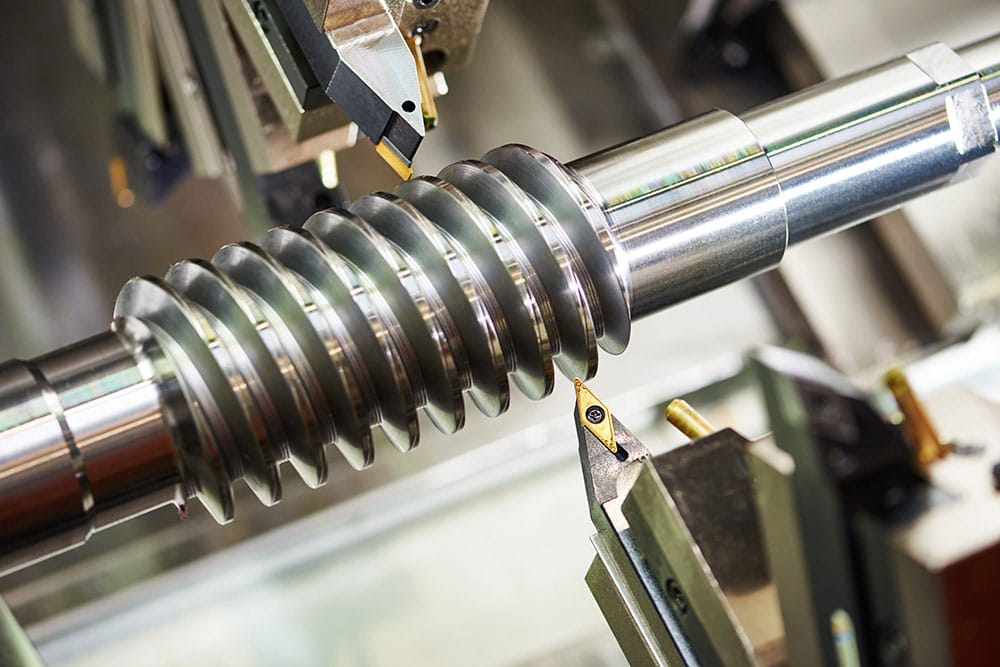
What is Precision Casting?
Precision casting refers to the general term for the process of obtaining precision-sized castings. Compared with the traditional sand casting process, the castings are obtained by precision casting have more precise dimensions and better surface finish. Its products are precise, complex, and close to the final shape of the part. Can be used directly without processing or processing. It is an advanced process of near-net-shape. And it can be suitable for low quantity request orders.
It includes investment casting, ceramic casting, metal casting, pressure casting, lost foam casting.
Precision casting Commonly used is investment casting, also known as lost wax casting. It is widely used for producing ferrous and nonferrous metal casting.
The investment mold is made by using a suitable investment material such as paraffin. The refractory coating and the refractory sand process are repeated on the investment mold. Hardened shell and dry. The internal melting mold is then melted off to get a cavity. The baked shell is obtained to get sufficient strength. The residual investment material is burned off and the desired metal material is poured. Solidification, cooling, shelling, sand cleaning. Thereby obtaining a high-precision finished product. Heat treatment and cold working and surface treatment according to product requirements.
Additionally, in both design and material choice of castings, Precision castings have huge freedom. It allows many types of steel or alloy steel for investment. So on the casting market, Precision casting is the highest quality castings.
Precision casting also faces a cost of molding and time. Each casting producing, requires a mold and one wax pattern. It will take more time and separate costs. So it is not a good cost-effective for low quantity products.
Precision casting has many process steps, so it will take more time for each casting. If with a flow line to show. It is :
Waxing (wax mold)—repair wax—-wax inspection—-group tree (wax module tree)—shell (first paste, sand, re-slurry, finally Mould air drying)—Dewaxing (steam dewaxing)——-Mould roasting–chemical analysis–casting (casting molten steel in the mold shell)—-vibration shelling— Cutting and pouring of casting and pouring rod—-grinding gate—initial inspection (hairy inspection)—shot blasting—–machining—–polishing—finish inspection— Storage
Next is the main Precision casting process introduction.
What is Precision Casting Processes
Step 1. MOLD DESIGN
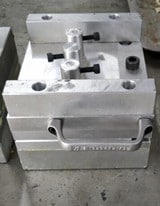
As per the drawing, our engineer will finish the mold design. The mold is purchased from a mold factory.
Step 2. WAX INJECTION
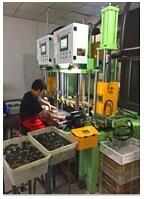
The wax is being injected by a machine. Wax design of the desired castings is produced by injection molding. This process is called patterns.
Step 3 . ASSEMBLY TREE
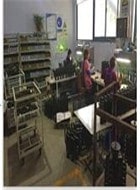
The patterns are attached to a central wax stick, called a sprue, to form a casting cluster or assembly tree.
Step 4. SHELL MAKING
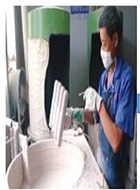
The shell is built by immersing the assembly in a liquid ceramic slurry and then into a bed of extremely fine sand. Up to SIX layers may be applied in this manner. The shell will be dry in each layer making.
Step 5. DEWAX
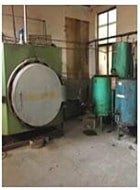
Once the ceramic is dry, then heating. The wax will be melted out. The melted wax will be flow out from the shell.
Step 6. CASTING
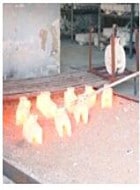
In the conventional process, the shell is filled with molten metal by gravity pouring. As the metal cools, the parts and gates, sprue, and pouring cup become solid casting.
Step 7. KNOCKOUT
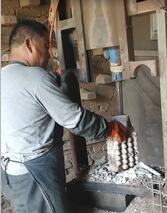
When the metal has cooled and solidified, the ceramic shell will be broken off by vibration or a knock-out machine.
Step 8. CUT OFF
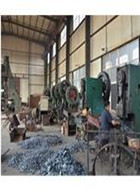
The parts are cut away from the central spruce using a high-speed friction saw.
Step 9. GRINDING
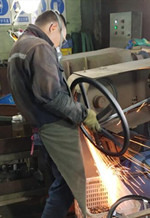
After the casting was cut off. The casting pouring part will be ground carefully.
Step 10.Inspection and Post Treatment.
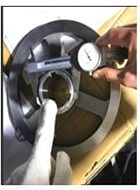
The casting will be inspected by the inspector as per the drawing and quality request. If there are unqualified parts. It will be repaired and inspected again.
Step 11. FINISHED CASTINGS
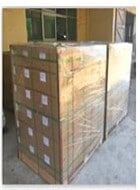
After surface finishing operations, the metal castings become identical to the original wax patterns and are ready for shipment to the customer.
For Precision Investment Casting Process Documents, you can download the precision investment casting process pdf as below:
If you are a precision manufacturer, you should know some Influence accuracy factors
Influence accuracy factor
Under normal circumstances, the dimensional accuracy of precision castings is affected by many factors such as the structure of the casting material, molding, shelling, roasting, and casting. Any one of the links set up and unreasonable operation will change the shrinkage rate of the casting. The dimensional accuracy of the casting has deviated from the requirements. The following are factors that can cause defects in the precision of precision castings:
(1) The influence of the structure of the casting.
a. The casting has a thick wall and a large shrinkage. The casting has a thin wall and a small shrinkage.
b. The free shrinkage rate is large, which hinders the shrinkage rate.
(2) The influence of casting material.
a. The higher the carbon content of the material, the smaller the line shrinkage. The lower the carbon content, the greater the line shrinkage.
b. The casting shrinkage of common materials is as follows: casting shrinkage K = (LM-LJ) / LJ × 100%, LM is the cavity size, and LJ is the casting size. K is affected by the following factors: wax mold K1, casting structure K2, alloy type K3, casting temperature K4.
(3) The influence of mold making on the shrinkage of the casting line.
a. The effect of the wax temperature, the wax pressure, and the dwell time on the size of the melt is the most obvious. Followed by the wax pressure. The holding time has little effect on the final size of the investment after the injection molding is ensured.
b. The linear shrinkage of the wax (molding) material is about 0.9-1.1%.
c. When the investment mold is stored, further shrinkage will occur, and the shrinkage value is about 10% of the total shrinkage. However, after 12 hours of storage, the size of the investment was substantially stable.
d. The radial shrinkage of the wax mold is only 30-40% of the shrinkage in the longitudinal direction, and the effect of the wax temperature on the free shrinkage is far greater than the effect on the resistive shrinkage (the optimum wax temperature is 57-59 ° C, The higher the temperature, the greater the shrinkage).
(4) The influence of the shell material.
Zircon sand and zircon powder are used because of their small expansion coefficient, which is only 4.6×10-6/°C, so they can be ignored.
(5) Effect of shell baking.
Since the expansion coefficient of the shell is small, when the shell temperature is 1150 ° C, it is only 0.053%, so it can be neglected.
(6) The influence of casting temperature.
The higher the casting temperature, the greater the shrinkage. The pouring temperature is low and the shrinkage rate is smaller. Therefore, the pouring temperature should be appropriate.
Advantages of Precision castings
Perfect-Surface Finish
The investment casting process provides a far superior surface finish as compared to forgings and sand castings. Sometimes this is important and can avoid machining or other finishing operations.
Closer to finished part designs
Investment Castings provide near net shapes for manufactured parts, thus eliminating or reducing machining costs. Holes, undercuts, slots, and other difficult detail that cannot be had with other processes can often be provided. An added benefit of near net shape is the savings on material, especially with expensive alloys such as nickel and cobalt alloys.
Tighter Tolerances
Due to the nature of the process, Investment Castings can be held to much tighter tolerances than sand castings or forgings.
Competitive Tooling Costs
Initial charges for the investment casting tooling are often less expensive than those for sand castings.
Thin wall castings
The investment casting process is capable of more reliable castings with much thinner walls than sand castings. Advantages include substantially fewer scrap rates and castings that weigh less due to the thinner wall capability.
Less casting defects
Being a cleaner process than sand molds, investment castings, generally, provide a much higher percentage of defect free-castings.
Typical Precision Casting
Precision casting products are used in all industrial sectors, especially electronics, petroleum, chemical, energy, transportation, light industry, textiles, pharmaceuticals, medical equipment, pumps and valves.
Precision casting products:
Aluminum casting: general aluminum casting | aluminum box
Copper and aluminum castings: copper plates, copper sleeves | precision copper castings
Steel castings: large steel castings | small steel castings | precision steel castings | CDL1 | CGAS | CGKD | CGKA | CGA
Copper and aluminum castings
Ferro Tungsten
China Precision Casting Foundry
We are a China precision casting corporation located in Shandong. With a precision casting process, we can cast nearly 300 alloys. Our metals include stainless steel, tool steel, carbon steel, ductile iron, aluminum, copper, brass, and other alloy steels. Precision casting is suitable for complex and detailed part designs, such as impellers. Because it uses lost wax ceramic shells. Its patterns were injection molded in advance. After pouring, it can be finished. If a more perfect request, it can be made by machining and post-treatment.
With 23 years of history, we have made a range of high-grade investment and precision casting. Our business core is to provide quality precision castings with high working performance. Besides these, we can also provide precision die casting, precision aluminum casting, precision steel casting. We would like to be your reliable supplier for your precision cast parts. Our engineered precision casting department will give you a complete casting proposal about product design, material choice, machining details, etc for your reference.
If you want to get more details about what is precision casting or have precision casting projects needs, kindly contact us freely. email us at [email protected]