Sand casting bronze is a popular manufacturing process that uses either natural or synthetic sand and bronze or bronze alloys to produce high-quality items. The process involves a series of steps that require workmanship nourished by years of experience.
In general, sand casting is a fool-proof and reliable casting method that has been relied upon for centuries.
What is Sand Casting Bronze?
Sand casting bronze is the bronze output when a person uses the famous sand casting method to create. The sand casting process is among the oldest and most used methods of making products out of metal. It has been in use since 1818.
Features
Sand casting is a versatile, inexpensive, easy, and cost-effective method. Aside from this, it also allows for the creation of complex shapes and large parts. It also has a relatively shorter lead time compared to other metalwork methods. Lastly, sand casting allows for the recycling of scraps instead of throwing them away.
A sand casting of bronze and bronze alloys is used for a variety of industries and applications. This article will discuss more specific details of the applications in the next section.
Sand Casting Bronze Main Applications
Bronze sand casting is suitable for a wide range of projects and industries such as the following:
- Chemical, petrochemical, oil and gas, heavy machinery, marine, and water treatment industries;
- Parts and components of hardware
- Machinery, aerospace, heavy equipment, and hydraulic equipment.
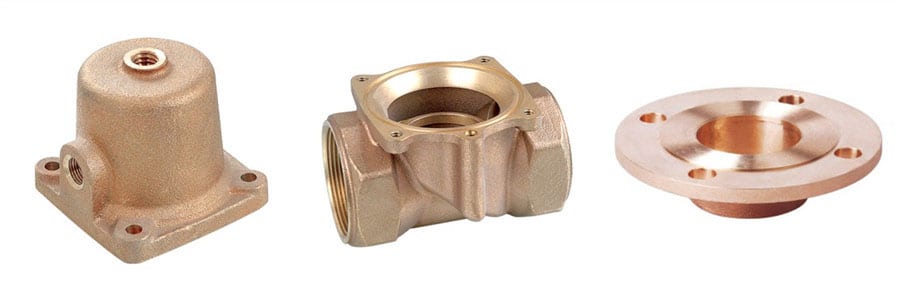
Types of Sand Casting Bronze
There are three main types of bronze sand casting. This section details these types and their applications.
- Aluminum bronze . Aluminum bronze is usually composed of 9-12% aluminum and 4-6% iron and nickel. The rest is pure bronze. This material boasts corrosion and wear resistance, high strength, and toughness.
It is used in the chemical, petrochemical, oil and gas, heavy machinery, marine, and water treatment industries. It is also ideal for connectors, nuts, fasteners, hardware, pumps, valve components, cams and shafts, gears, sleeve bearings, machine tool ways, and wear parts.
- Manganese and white manganese bronze. These two types of alloys are composed of 55 to 65% copper, 20 to 25% zinc, 1 to 5% manganese, and 1 to 5% iron. They are popular for their resistance to corrosion, high strength, high wear, and good mechanical properties.
These alloys are typically used for screw-down nuts, slow-speed heavy load bearings, gears, cams, propellers, machinery parts substituting for steel or malleable iron, ornamental castings, and marine hardware.
- Silicon bronze . Silicon bronze is a bronze alloy made of 96% bronze and 4% silicon and other elements. Because of resistance to corrosion, strength, and easy machinability and casting. Silicon bronze is best used for ball bearings, bearing cages, raceways, spacers, gears, and valve parts. It is also used for machinery, aerospace, heavy equipment, and hydraulic equipment.
Sand Casting Bronze Process
To create bronze products using the sand casting method, most foundries use the steps detailed below:
Step #1. Using wax or clay, the worker creates the original mold for the product.
Step #2. Depending on the product’s shape, and size, the model is cut into more manageable pieces. This step may be necessary for some products but may also be skipped for others.
Step #3. Once the original model has been separated into more manageable pieces, the next step is to cover the parts in a slurry. The slurry should be made of materials that are easily removed from the original model.
Step #4. Once the slurry has dried, the mold is separated, and the original pieces are removed. The mold is then put back together for the next step.
Step #5. A bronze master model is then poured into the mold.
Step #6. The unwanted lines and marks are removed to achieve a smoother finish and a seamless fit for the individual parts.
Step #7. The individual parts are then pressed into large casting sand blocks where a second block is fitted over the first one and pressed.
Step #8. After the blocks are separated and the master model is removed.
Step #9. Vents are cut into the sand, so the bronze flows freely and evenly into the mold. This also allows hot gasses to escape.
Step #10. Slurry or sand is placed in the center of the larger pieces to cut the use of bronze.
Step #11. The blocks are reassembled and strapped together.
Step #12. Molten bronze is poured inside. The required bronze casting temperature is about 1700°F, which is the temperature when bronze melts.
Step #13. The metal should cool and harden for some time. Once done, the pieces are then removed from the sand. This step may require the use of a chisel, hammer, and file.
Step #14. Once filed, the parts can be pinned or bolted together to create the finished product.
The bronze master model can typically be used up to twenty times before it begins to lose its details.
Sand Casting Bronze Foundry and Supplier
JC Casting is the leading sand casting bronze foundry and supplier, with both local and international deals. They provide a wide range of services and materials to cater to all your metalworking needs. Such as design, molding, casting, machining, and heat treatment, alloy steel, carbon steel, stainless steel, and aluminum.
Aside from the materials and services that they offer, JC Casting is known for the following:
- Quality assurance. With JC Casting, rest assured that only the best materials and most skilled workers will cater to your needs.
- Various alloy materials . JC Casting provides the broadest range of alloy materials to choose from.
- Fast delivery . JC Casting works accurately, but they also work quickly and efficiently to deliver your finished products.
- Lower cost . JC Casting is one of the most affordable companies in the industry right now. They achieve this by thinking outside the box to create more innovative and more efficient castings. The budget is never a concern with JC Casting.
Conclusion
Sand casting bronze is a process that requires bronze and sand to produce high-quality items. Contact JC Casting or browse our website for more information about everything there is to know about sand casting bronze. Email us: [email protected]