Casting VS Forging
There are several different methods and techniques in manufacturing metal components.
Castings and forgings are 2 of them. What is casting or forging? What are the differences between casting and forging? Based on the end-use purpose of the metal part, different procedures use different methods to create the highest quality piece possible. This is the best choice!
But which one is more effective for their metal component and most cost-effective? To find out their differences between casting and forging. You will know which one is better for you. It will improve the excellence of your products.
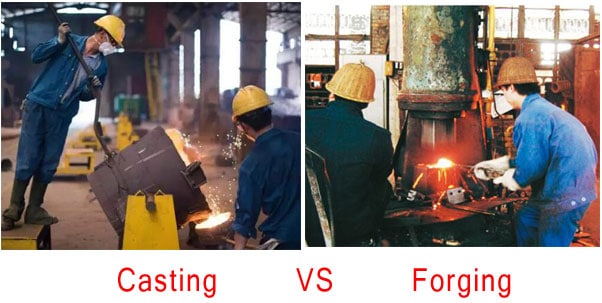
If you want to get reliable and durable products and suppliers, trust me. Learning this article. It is very useful.
What is casting?
Casting is the method where metal is heated until molten. Then pouring or injecting molten metal into a molded vessel to create the desired shape. If the component shape is a very large size, the casting process is beneficial. Because by using a mold, it is easy to get a net shape or similar net shape parts.
Sometimes the machining cost can be saved. Once the metal cools into the finished shape, we can do post-treatment to get more precision casting. The metalworker can finish the part with the details requested by hand or through further machining.
Metal casting processes can be classified by the type of mold or by the pressure used to fill the mold with liquid melted metal.
Depending on the correct selection of alloys, Casting can heat them to their greatest temperatures. Then get higher quality producing material with greater strength and wearability.
Fundamentals of Casting is a solidification process. So, the microstructure can be finely tuned. Such as grain structure, phase transformations, and precipitation. Yet, defects such as shrinkage porosity, cracks, and segregation are also intimately linked to solidification. These defects can lead to lower mechanical properties. Later heat treatment is often required to reduce residual stresses and optimize mechanical properties.
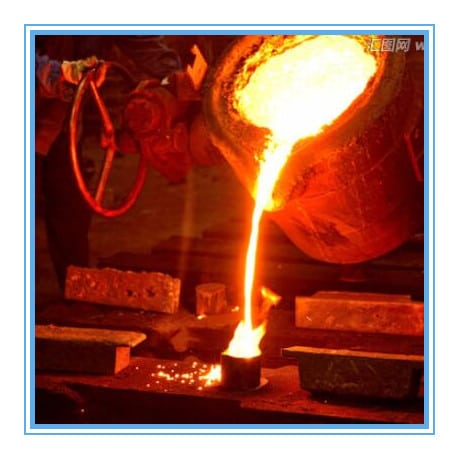
Advantages of Casting
- The melting of metal allows it to be formed into a greater variety of shapes. The part design is greater flexible.
- Cast parts are nearly always lighter than their forging counterparts.
- Initial results are often closer to design specifications. lessening time spent on secondary machining and processing
- Smaller production “runs” required
- For large and complex components – casting is a fantastic method of manufacture
- Complicated/complex parts are no problem
- Tooling is often less expensive than forge dies
- No real upper size limit in casting weight
- A large range of alloy choices. Alloys including Chrome, Nickel, and Mo can be added at the molten stage.
Casing Types:
- 1.Investment Casing
- 2.Sand Casing
- 3.Die Casing
For large, complicated, intricate, or otherwise unsuitable for the forging process wear parts and components, we can use castings
What is Forging?
Forging is a metal forming process. This process does not involve heating.
It is the application of thermal and mechanical energy to steel billets or ingots, then hammered and manipulated into the final desired shape. Forgings are generally stronger than castings.
But for forging Components can not be very complex. Because there are some limitations to the manufacturing capabilities of forging. Usually, if a component needs to be forged and also needs to meet certain size requirements, the component needs to be machined after it has been produced.
Forging can be performed under different temperatures: cold, warm, and hot, depending on the material. The process of forging is preferred where a component requires higher strength.
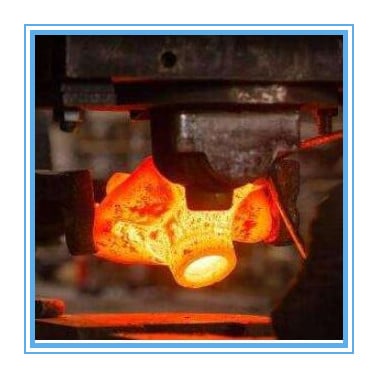
Forging results in metallurgical crystallization and grain refinement as a result of the thermal cycle and deformation process. This strengthens the resulting steel product particularly in terms of impact and shear strength. Forged steel is generally stronger and more reliable than castings and plate steel because the grain flows of the steel are altered, conforming to the shape of the part.
Advantages of Forging
- Superior structural integrity and mechanical strength
- Save cost than casting thanks to less intensive labor requirements and less involvement of material scrap
- Eliminates surface porosity along with voids and other defects
- The nature of forging excludes the occurrence of porosity, shrinkage, cavities, and cold pour issues
- Will handle impact better than castings
- Forging is more consistent in the yield of produced parts and in producing parts that are incredibly strong and ductile
- The tight grain structure of forgings making it mechanically strong. There is less need for expensive alloys to attain high-strength components.
- The tight grain structure offers great wear resistance
Types of Forging
1– Open die forging
Open die forging is one of the oldest forms of manufacturing. It is a traditional blacksmith method.
The billet is heated above the recrystallization temperature. ( ranging from 1000°C to 1300°C for steel). Then gradually shape it by skillful hammering or pressing of the workpiece to create the desired shape.
Open die forgings produce strong, durable parts in sizes that range from a few kgs to hundreds of tons.
As a result, it is a favorable method to produce large and simple parts. Such as bars, rings, blanks, hollows, and spindles. Open die forging is also a great chance for custom metal components as well.
2–Closed die forging
Closed die forging is the process where a pressing of forging stock is accurately and uniformly shaped into a die, or set of top and bottom dies, depending on the design requirements.
The alloy deformation is confined within the shaped cavity of the dies. Then to achieve the desired engineering configuration. Depending on such factors as complex multi-segmented precision wrap dies to simple two-piece conventional top-and-bottom dies.
The process by which the material is placed between two dies with upper & lower impressions designed for the desired shape of the forging.
Conventional forgings are produced through the use of a single pair of dies or with multiple impression dies.
Difference between Forging and Casting
For casting and forging, each process has its own advantages. One method is preferred for certain projects. While the other is better suited to others. Below we list out the main differences between casting and forging:
1: Strength Difference:
Casted material is low in strength as they are poured into a cavity which lets the material take its shape freely.
Forged materials are stronger. Because they have a definite grain structure that is pressed with force, increasing their mechanical strength.
2: Suitability for Hollow Shapes
Casting is often preferred for the production of material containing hollows spaces or cavities.
Forging excludes cavities and porosity from their compositions.
3: Uniformity Different:
The casted material is not always uniform.
Forged material can be made to a uniform structure-preserving consistency in shape.
4: Size Restrictions:
Casting doesn’t have any size or shape limitations. Because all materials will be melted before putting them into shape.
Materials weighing up to 50kgs can be forged. A higher power is required if the material to be forged is heavier than 50kgs. In this case, casting would be the alternative.
5: Level of Complexity
Casting can produce complex patterns and shapes. Forging is more focused on producing a uniform and simple material.
6: Cost Different:
Casting uses relatively inexpensive equipment. Machines used for forging such as heavy-duty industrial dies are more expensive.
Here is a research paper, researchers at the University of Toledo compared the differences between one type of product made both ways. the following conclusions were listed:
• The tensile strength of forged parts is 26% higher than that of cast parts.
• The fatigue strength of forged parts is 37% higher than that of cast parts.
• Cast iron exhibits only 66% of the yield strength of forged steel.
• Forged parts exhibit a 58% reduction in the area when pulled to failure. While cast parts exhibit a 6% reduction in area.
Conclusion
Via this article, you can understand the differences between Casting VS Forging well. You can check the product you want, then decide the process.JC Casting can provide the Casting and Forging products as per your request. If you have any inquiries, contact us today. You will get a prompt reply within 12 hours.