What is a Pump? Maybe it is a simple question. Maybe it is a highly complex question. To say simple, it is a concept only. To say complex, because its range is too huge and wide. This article is the fullest introduction to the topic of what is a pump.
What is a Pump?
A pump is a machine that pressurizes by some mechanism (usually a reciprocating or rotary type), transporting fluid from a low level (low pressure area) to a high level (high pressure area). Pumps can only transport substances with fluid as a medium, not solids. Fluids include water, oil, acid-base liquid, emulsion, suspoemulsion, liquid metal and other liquids, and can also transport gas.
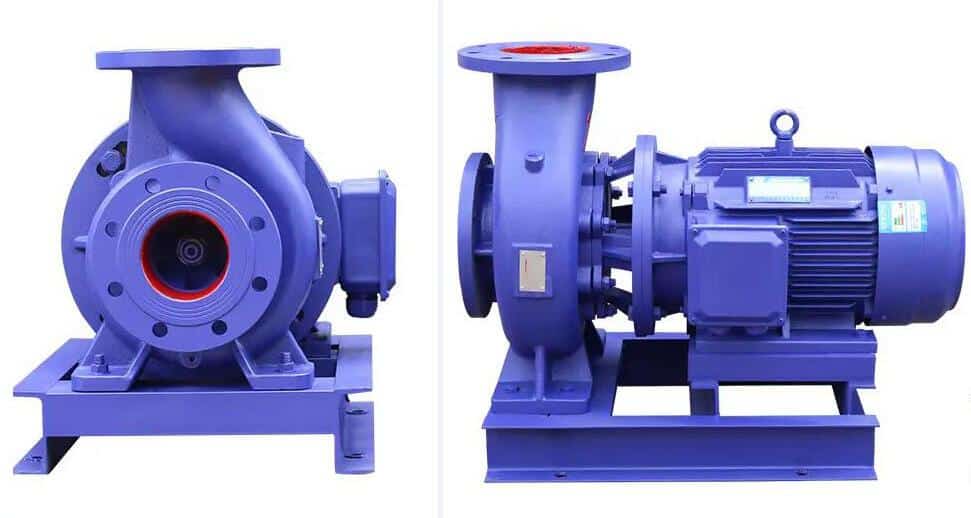
As a machine, a pump can be powered by a variety of energy sources. Such as physical operations, electricity, motors or wind. Meanwhile, pumps include a variety of sizes, from microscopic pumps to various large industrial pumps. Regardless of the size of the pump, all pumps deliver fluid from the pump’s inlet to the pump’s outlet by increasing pressure.
The structure of the pump is also not complicated. For example, a centrifugal pump is mainly composed of a pump body, an impeller, a sealing ring, a rotating shaft, a shaft seal box and other components. Each part can be finished by casting process. Then assembled into a complete pump.
As a foundry, many of JC ASTIGN’s castings are pump castings. We also introduce lower pumps based on our pump casting experience.
The main function of the pump
As a common machine, the function of the pump includes the following aspects:
- Transport fluids from low-pressure areas to high-pressure areas.
- Circulate fluid from one point to another.
- Can be used to increase the flow rate of the transport fluid.
- It increases the pressure or head of the pump to meet the required discharge pressure requirements.
- When the system loses pressure, a pump can be used to increase the pressure of the system to stabilize it.
The main performance parameters of the pump
The main performance parameters of the pump are flow rate, lift, shaft power, necessary NPSH, speed, etc.
(1) The flow rate of the pump
The quantity of liquid provided by the pump per unit time, there is volume flow Q, the unit is m3/s; there is mass flow G, the unit is kg/s.
(2) The lift of the pump
Lift is the energy increment per unit weight of the liquid transported from the pump inlet to the outlet. Usually expressed in H. The unit is m. Taking the water pump as an example, the lift of the water pump refers to the height at which the water pump can lift water.
(3) The shaft power of the pump
Shaft power is a term often used on pumps. It refers to the work given to the pump shaft per unit time under a certain flow and head. It is represented by P and the unit is kW.
(4) Speed.
The number of revolutions per minute of the pump, represented by n, in r/min.
(5) NPSH
The NPSH must be related to the internal flow of the pump, it is independent of the device parameters. It indicates the degree to which the pressure of the liquid drops in the inlet part of the pump. That is to say, in order to prevent cavitation of the pump, it is required that the unit weight of the liquid at the pump inlet has excess energy exceeding the vaporization pressure head.The smaller the required NPSH, the better the pump’s cavitation resistance.
There is an interdependent relationship between the various performance parameters of the pump. And the viscosity of the liquid conveyed by the same pump is different. The relationship between its performance parameters will also change.
For example, a power pump, as the viscosity of the liquid increases, the lift and efficiency of the power pump decrease, and the shaft power increases. It is also for this reason that in order to improve the conveying efficiency in the industry, the liquid with high viscosity will be heated to reduce the viscosity.
Classification of pumps
There are many types of pumps, and there are many ways to classify them. For example
- According to the working principle: positive displacement pump, dynamic pump and other types of pumps.
- According to the nature of the conveying fluid: water pump, oil pump and mud pump.
- According to the driving method: electric pump and hydraulic pump.
- According to the structure with or without shaft: linear pump and traditional pump.
- According to the structure: single-stage pump and multi-stage pump.
- According to the application: boiler feed pump and metering pump.
Although there are many types of pumps, the most commonly used are positive displacement pumps and power pumps. At the same time, there are many types of positive displacement pumps and dynamic pumps. The following types of pumps are described in detail.
Positive displacement pump
The positive displacement pump uses the reciprocating or swirling motion of the working parts in the pump cylinder to periodically increase and decrease the working volume to suck and discharge liquid. The positive displacement pump mainly increases the pressure of the liquid through the extrusion of the working parts.
There are also many types of positive displacement pumps. Such as reciprocating pumps, rotary pumps, diaphragm pumps, piston pumps, plunger pumps, gear pumps, screw pumps and water ring pumps (water ring vacuum pumps).
Reciprocating pump
A positive displacement pump in which the working parts reciprocate in the pump cylinder is called a reciprocating pump. The suction and discharge processes of the reciprocating pump are alternately performed in the same pump cylinder. And controlled by a suction valve and discharge valve.
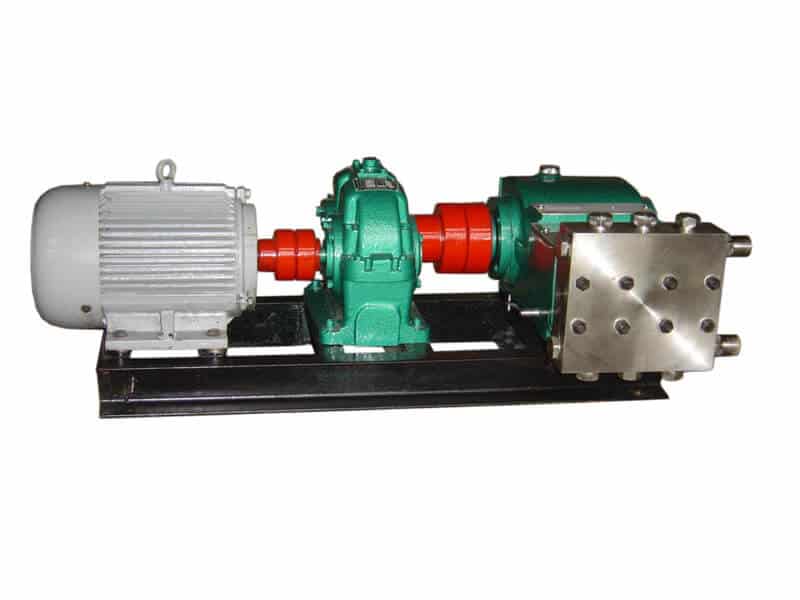
The main features of the reciprocating pump are:
- Can reach very high pressure, and the pressure change hardly affects the flow. Because of this feature, the reciprocating pump can provide constant flow.
- The reciprocating pump has self-priming ability. Can deliver liquid and gas mixtures. Specially designed reciprocating pump. It can also transport mud, concrete, etc.
- The flow and pressure of the reciprocating pump have large pulsation, especially the single-acting pump. Double-acting pumps and multi-cylinder pumps can be used to improve flow unevenness.
- The speed of the reciprocating pump is low and the size is large. The structure is complex and requires a special pump valve.
Rotary pump
The rotary motion of the working parts in the pump cylinder is called a rotary pump. The rotary pump sucks fluid through the rotation of working parts such as gears, screws, and vane rotors. Finally, the fluid is squeezed to the discharge pipe and output. Most rotary pumps are used to transport oily liquids and in hydraulic transmission systems.
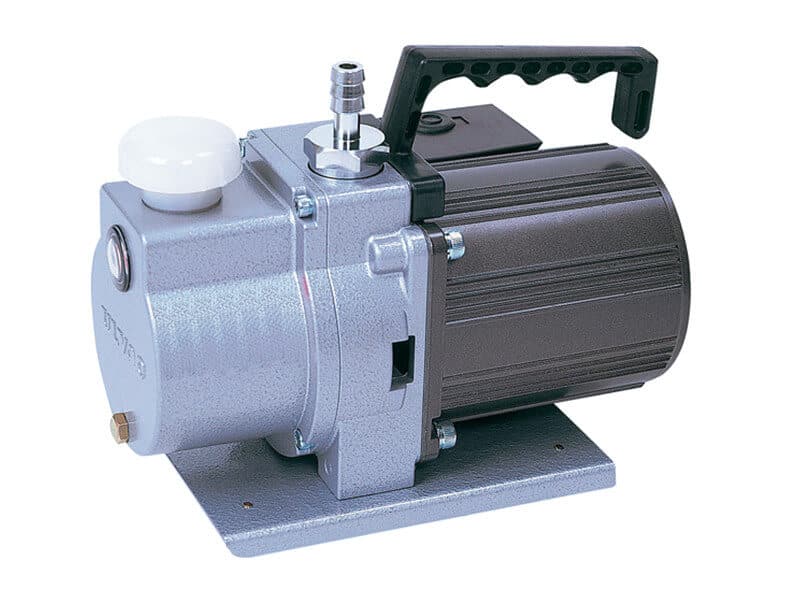
The rotary pump has the following characteristics:
- The rotor performs rotary motion without impact. The number of revolutions is high. Therefore, its structure is compact and its volume is smaller than that of a reciprocating pump.
- Unlike reciprocating pumps, rotary pumps generally have no pulsation. or only small pulsations.
- Compared with the reciprocating pump, the discharge pressure of the rotary pump is smaller. Flow and efficiency are lower. Therefore it is also only suitable for transporting small quantities of liquids.
Diaphragm pump
The diaphragm pump uses compressed air as the power source. Reciprocating deformation of the film results in a volume change. Thereby suction and discharge of liquid fluid. Its working principle is similar to that of a plunger pump. Diaphragm pumps are often used where power is not available.
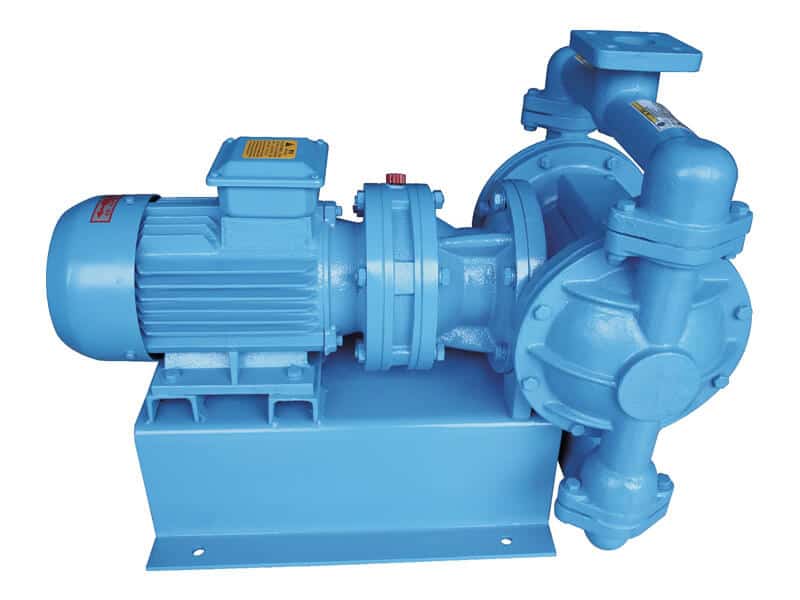
There are four kinds of materials used in the diaphragm pump. Engineering plastics, stainless steel, aluminum alloy, cast iron. Can be produced using the casting process. Diaphragm pumps use different materials according to different fluid media. Such as fluorine rubber, nitrile rubber, polytetrafluoroethylene, neoprene, polytetrahexaethylene, etc.
The main features of the diaphragm pump:
- The diaphragm pump uses compressed air as kinetic energy and will not generate sparks. Can be used in flammable and explosive environments.
- The diaphragm pump is easy to operate and has no complicated control system.
- Diaphragm pumps have a wide range of applications. It can be used for various corrosive liquids, liquids with particles, high viscosity, volatile, flammable and highly toxic liquids.
- The diaphragm pump has no mechanical seal and no lubricating oil. Maintenance is simple and convenient.
Piston pump
Piston pumps are positive dislocation pumps. It makes the reciprocating motion of the piston, so that the volume of the pump cavity changes to realize the suction and discharge of the liquid. Piston pump consists of pump cylinder, piston, inlet and outlet pipes, inlet and outlet valves, and connecting rods.
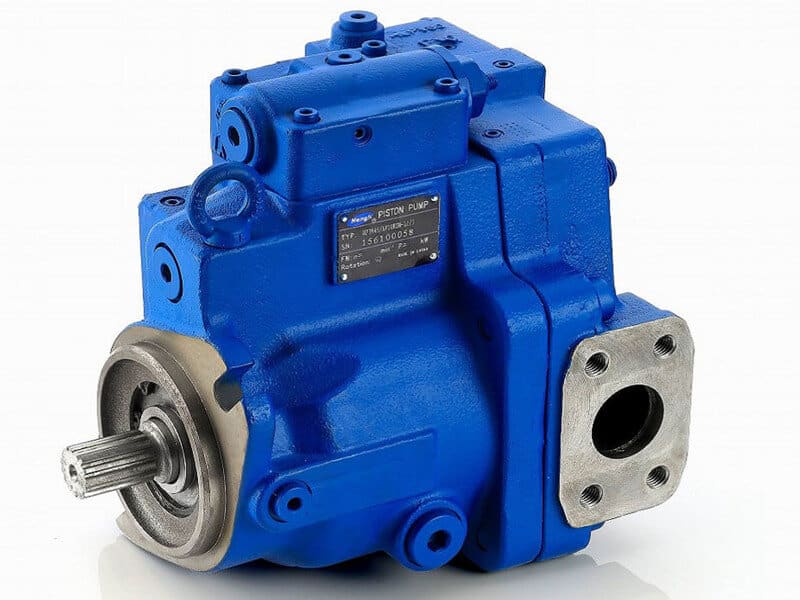
The main features of the piston pump:
- High exhaust efficiency, fast speed and small volume.
- Simple structure and easy maintenance;
- The system is simple and does not require external accessories such as water tanks and control valves;
- Applicable to a wide range of work. It can transport oil emulsion without solid particles at room temperature. It can also transport high-temperature tar, mineral sludge, high-concentration mortar, high-viscosity liquid, etc.
- But its exhaust continuity is poor. The noise and vibration are large at high speed, and it is suitable for short-term high-speed work.
Plunger Pump
The plunger pump relies on the reciprocating movement of the plunger in the pump cylinder. So that the volume of the sealed pump cavity changes to realize the suction fluid. The plunger pump is an important device in the hydraulic system. Often used in hydraulic presses, construction machinery and ships.
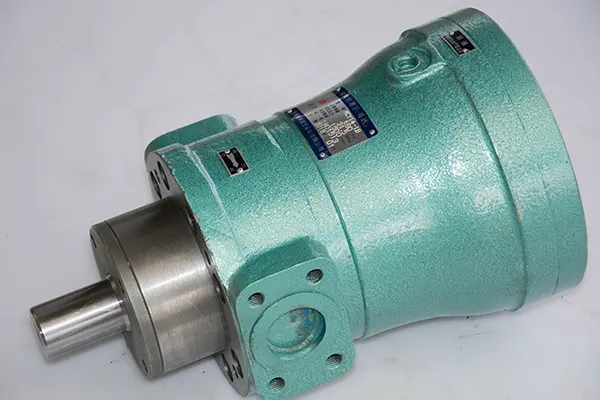
The main features of the plunger pump:
- The plunger pump has high rated pressure, high speed and compact structure.
- The efficiency of the plunger pump is high. Its volumetric efficiency is around 95%. The overall efficiency can reach about 90%.
- Variables are convenient and have many forms. And the flow adjustment is convenient.
- The structure is more complex and the number of parts is large. The process requirements are high and the cost is more expensive.
Gear pump
The gear pump belongs to the rotary positive dislocation pump. It consists of two closed spaces composed of two gears, a pump body and a front and rear cover. It conveys liquid or pressurizes it through the change and movement of the working volume formed between the pump cylinder and the meshing gear.
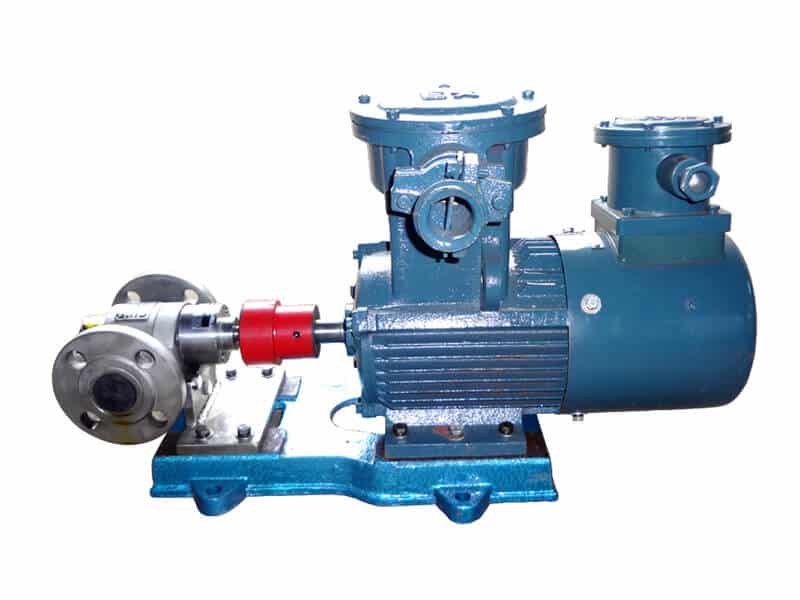
The specific principle can refer to the following:
- When the gear rotates, the space on the disengagement side of the gear increases from small to large, forming a vacuum and sucking the liquid.
- When the space on the meshing side of the gear becomes smaller, the liquid will be squeezed into the pipeline.
The main features of the gear pump:
- The gear pump is small in size, light in weight, simple in structure and easy to maintain.
- The gear pump does not contain a valve, so it can transport thick fluids.
- The gear pump has better self-priming performance.
- The flow and pressure pulsation are large and the noise is large.
screw pump
The structure of the screw pump is simple. Consists of pump housing, screw blades and shaft. The lower ends of the helical blades are in contact with the fluid to be conveyed. When the helical blade rotates, the fluid moves in the direction of axial helical rise until it flows out.
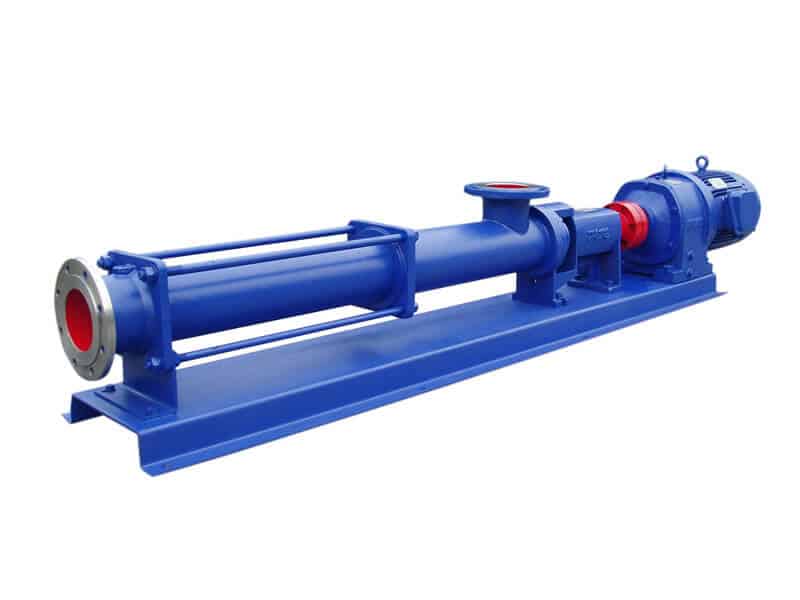
The screw pump has the following characteristics:
- The structure of the screw pump is simple, easy to manufacture, easy to repair and maintain.
- The screw pump can transport water containing solids. It is usually used for irrigation, drainage, and lifting of sewage and sludge.
- Can transport high-viscosity fluids. such as crude oil.
- The screw pump has large flow and high efficiency.
- Low lift and low speed.
Water ring pump (water ring vacuum pump)
The water ring pump is a kind of rough vacuum pump. There is an eccentric rotor in the water ring pump, and the eccentric rotor has fixed blades. The water is thrown against the stator wall by the rotation of the vanes, and a liquid ring is formed. The suction, compression and exhaust are realized by changing the volume of the pump cavity through the liquid ring and vanes.
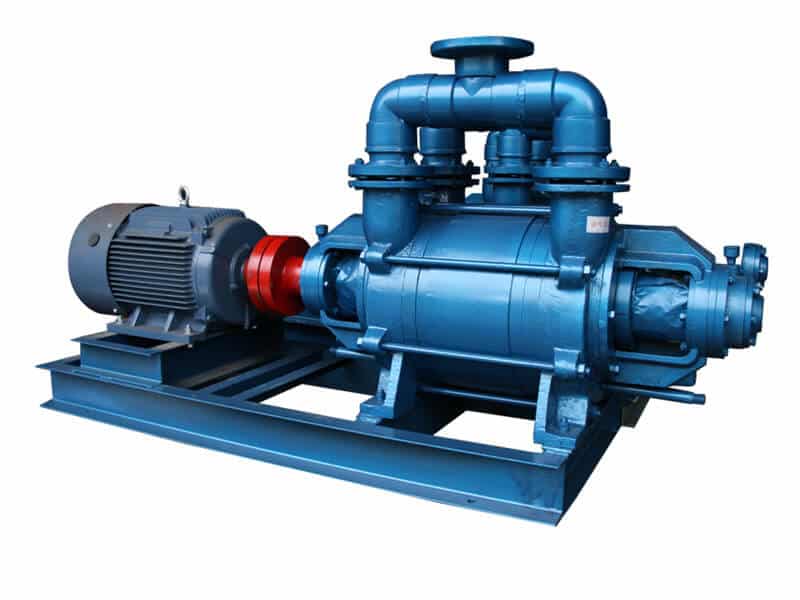
The main features of the water ring pump:
- The compression temperature is low, so it is suitable for transporting flammable and explosive gases.
- The water ring pump has a wide range of applications. It can be used in coal mines, chemicals, pharmaceuticals, mining, beer, building materials, plastics, metallurgy, electrical appliances and other industries.
- The structure is simple, the manufacturing precision is not high, and it is easy to process.
- The water ring pump is easy to operate and easy to maintain.
- The efficiency of the water ring pump is low, generally between 30% and 50%.
Powered pump
Power pumps rely on rapidly rotating impellers (vanes) to act on the fluid. The mechanical energy is transferred to the liquid, so that the kinetic energy and pressure energy of the fluid are increased. The final realization of the transport of fluids. Power pumps are also known as vane pumps and impeller pumps.
Power pumps can be divided into centrifugal pumps, axial flow pumps, partial flow pumps and vortex pumps. The most common power pump we usually use is the centrifugal pump.
Centrifugal pump
The basic structure of a centrifugal pump is composed of pump body, impeller, pump bearing, pump shaft sealing ring and other components. Its working principle is to drive the impeller to rotate through the pump shaft. So that the water has a centrifugal motion to realize the transportation of fluid.
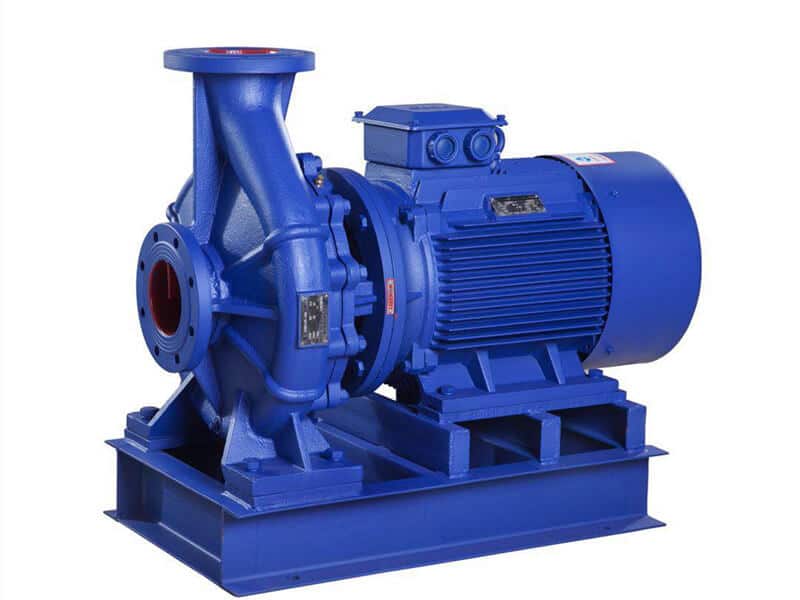
The main features of centrifugal pump:
- High efficiency of centrifugal pump. The flow range is wide and the performance is smooth without fluctuations.
- The rotational speed of the centrifugal pump is high. The transmission method is relatively simple and can be directly linked to the motor.
- The centrifugal pump has a simple structure and is easy to operate and maintain.
- The centrifugal pump delivers fluid without pulsation.
- The viscosity of the fluid has a great influence on the centrifugal pump. When the viscosity of the liquid increases, the flow, head, suction and efficiency of the centrifugal pump will be significantly reduced.
Axial flow pump
The main structure of the axial flow pump includes: impeller, pump casing, pump shaft, guide vane, guide vane body, suction pipe, water outlet pipe, coupling and other components. It mainly produces force on the liquid by rotating the blades of the impeller, so that the liquid flows along the axis direction.
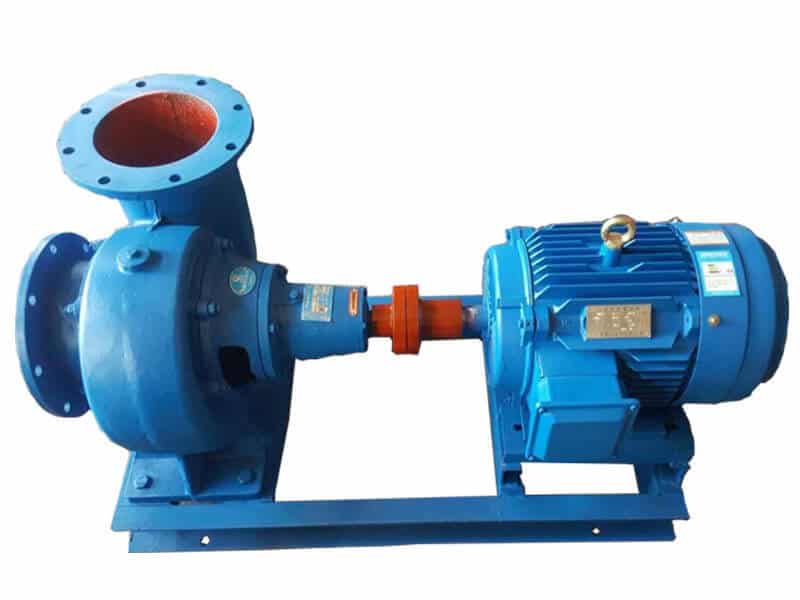
The main features of axial flow pump:
- The axial flow pump can transport clean water and mild sewage, and the medium temperature can reach 40℃.
- Axial flow pump is suitable for large flow and low lift.
- Axial flow pump is different from centrifugal pump. The smaller the flow rate of the axial flow pump, the greater the shaft power. So, the valve should be opened to start.
The impeller of the axial flow pump is generally immersed in the liquid. So, cavitation does not need to be considered. There is also no need to prime the pump with fluid at start-up.
Partial flow pump consists of pump body, suction pipe, impeller, high-speed shaft, inducer and other components. It is a high-lift, small-flow high-speed centrifugal pump. When the partial flow pump works, the liquid enters the impeller through the suction pipe, and then outputs a small amount of liquid. The rest of the liquid rotates at high speed in the annular channel. And the relative speed with the impeller is very low, and the hydraulic loss is small.
The main features of the partial flow pump:
- Partial flow pump is suitable for the occasion of conveying small flow and high lift fluid.
- The flow-head performance curve of the partial-flow pump is flat, and it maintains a relatively stable outlet pressure when the flow changes. This solves the overpressure problem of ordinary centrifugal pumps at small flow rates.
- The pump body of the partial flow pump has no front and rear cover plates, and the blades are straight and radial. Its liquid resistance loss is small.
Vortex pump
The inside of the pump body of the vortex pump is an annular flow channel. It is mainly composed of pump body, impeller, pump cover and other components, and the structure is relatively simple. When the liquid to be transported enters the pump body, the liquid repeatedly makes a vortex motion in the vanes and the flow channel of the pump body.
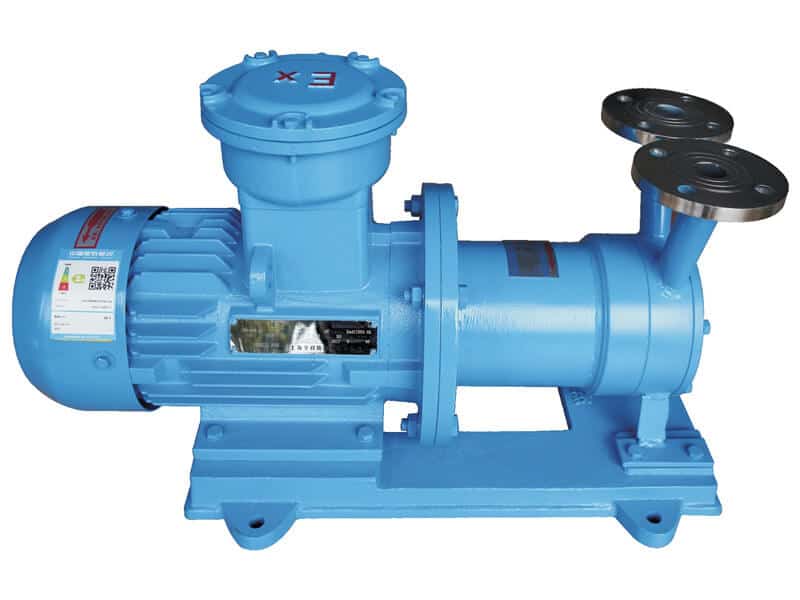
The main features of the vortex pump:
- The vortex pump is the simplest high-lift pump. In the case of the same size, its lift is 2 to 4 times higher than that of a centrifugal pump. In the case of the same head, its size is much smaller than that of a positive displacement pump. The structure is also much simpler.
- It is difficult to make a vortex pump into a high-power pump. The impact loss of the liquid to be transported in the annular flow channel is relatively large. So, the efficiency of the vortex pump is very low. Its efficiency usually ranges from 15% to 40%.
- Some vortex pumps can also transport gas and vapor-liquid mixtures.
- Some vortex pumps have self-priming ability.
- The vortex pump is mainly suitable for conveying acid, alkali and other corrosive and volatile liquids with high head and small flow.
There are many types of pumps. Each pump can choose the appropriate material according to the material of the conveyed fluid, and then complete it through the casting process. Common materials for our cast pumps include aluminum, stainless steel, carbon steel and brass. Of course, the casting material required by the customer is also customized. Such as flexible cast iron, dark iron, heat-resistant tempered steel and other composite steels. The accessories of each pump can be cast in different metal materials and then assembled.
Pump application industries
Pumps are one of the main products in the machinery industry, and they are classified as general-purpose machinery. The operation of pumps is required everywhere in our lives, in industry, in agriculture and in the medical industry.
Application of pumps in the chemical industry
Most of the raw materials, finished products and semi-finished products of chemicals and petroleum are liquids and require complex technological processes.
The main functions of pumps in the chemical industry are: transporting liquids, providing pressure flow for chemical reactions, and adjusting temperature.
Applications of pumps in agriculture
In agriculture, a large number of pumps are required every year, which can account for more than 40% of the total pump production. These pumps are commonly used for irrigation and drainage in agriculture.
Application of pumps in mining
Pumps are also common equipment in the mining and metallurgical industries. It can supply water in the process of smelting and rolling. It can also drain mine.
Application of pumps in the power industry
In the power system. Thermal power plants need a large number of pumps. Including water pumps, condensate pumps, and circulating water pumps. In nuclear power plants, nuclear main pumps, secondary pumps, tertiary pumps are needed.
Applications of pumps in the medical industry
Pumps can be used in pharmaceutical development and manufacturing processes. And can be used as artificial replacements for body parts. such as artificial hearts.
Applications of pumps in the energy industry
Pumps can be used to transport oil and gas. It can also be used in cooling towers, heating, ventilation and air conditioning systems.
The production process of the pump
Pumps can be divided into casting pumps, forging pumps and stamping pumps according to different processing techniques.
Our most common pump machining process is casting. Casting pumps do not need complicated processes and high-tech equipment. It also has the following advantages:
- Casting pumps are inexpensive to produce.
- Casting is also an environmentally friendly process. The cast mold material can be used repeatedly.
- Casting can produce pump casings and components of different shapes.
- The size of the pump produced by casting is accurate. There will not be too many errors.
- Cast pumps are strong enough. Can hold a lot of solids through without deforming the casing of the pump
The pump casting process improves the strength and corrosion resistance of the pump. For example, the casing of the pump is made of cast iron as the casting raw material. It not only increases the corrosion resistance of the pump room, but also makes the pump casing have a strong ability to withstand stress.
Pump castings are also available for various parts of the pump. Such as impellers, valves, etc. Different casting materials can be selected according to different delivery fluids, and then assembled. This also greatly reduces the cost of the pump and is also the method of choice for many pump equipment manufacturers.
Principles of pump selection
The selection of the pump type can be considered according to the performance parameters, the nature of the conveying fluid, the technological process, the water supply and drainage requirements and other factors.
Performance parametersBefore selecting a pump, first consider the performance parameters of the pump. Including flow, head, temperature, cavitation flow, suction lift, etc.
Flow rate
Flow rate is one of the important performance data for pump selection. It is directly related to the delivery capacity of the pump. When choosing a pump, take the maximum flow as the basis and take into account the normal flow. If there is no maximum flow, 1.1 times the normal flow can be taken as the reference.
Pump lift
Pump lift is another important performance data for pump selection. Generally, it is necessary to enlarge the 5%-10% margin and then choose.
conveying fluid properties
The properties of the transport fluid include physical properties, chemical properties and other properties. Physical properties include temperature, density, viscosity, and solid particle diameter and gas content in the fluid. Chemical properties include chemical corrosiveness, toxicity, and flammability and explosion of fluids.
Please refer to the following for specific choices:
- Pumps for transporting flammable, explosive, toxic or precious media. Use reliable or leak-free pumps with shaft seals. Such as magnetic drive pump, diaphragm pump, canned pump.
- Pumps for transporting corrosive media. Select pump convection parts using corrosion-resistant materials.
- Pumps for conveying medium containing solid particles. Wear-resistant materials are required for the convection parts of the pump.
Type of pump
There are many types of pumps, and we can choose a type of pump in combination with a variety of conditions.
According to the flow rate, you can choose a single-suction pump or a double-suction pump.according to the height of the lift, choose a single-stage pump or a multi-stage pump, a high-speed pump or a low-speed pump (air conditioning pump). The efficiency of a multi-stage pump is lower than that of a single-stage pump. such as a single-stage pump. When both pumps and multi-stage pumps can be used, single-stage pumps are used first.
Different pumps can be selected according to the properties of the fluid. For example, determine the clean water pump or the impurity pump, the hot water pump or the oil pump, the chemical pump, the corrosion-resistant pump or the non-clogging pump.
If the pump needs to be installed in an explosion area, the corresponding explosion-proof motor should be used according to the level of the explosion area.
Pumps can also be selected based on various other conditions. Such as terrain conditions, water level conditions, operating conditions, etc. The type of pump can choose horizontal, vertical and other types. Other types of pumps include in-line, submersible, submerged, non-clogging, self-priming, geared, etc.
The size of the pump
For the normal operation of the pump, generally only one large pump is used, and two small pumps are not selected.In the case of the same head and flow, a large pump is equal to two small pumps working in parallel, and the efficiency of the large pump is higher than that of the small pump, which can reduce the cost.
If the flow rate is too large and one pump cannot reach this flow rate, two pumps can be considered for parallel cooperation.
If the pump needs to run continuously for 24 hours, three pumps should be spared. One for operation, one for backup and one for maintenance.
Pump casting manufacturers
As a foundry, one of JCcasting’s core strengths is the production, machining and finishing of pump component castings. We can provide cast pump casings. Impeller casting, pump seat and pump installation. Our cast pumps include centrifugal pumps, fire pumps, submersible pumps and mud pumps. We can also provide other pump castings for petrochemical, oil field, oil extraction and refining, sewage treatment, strong waste treatment and other enterprises.
We can also provide custom (OEM) pump castings. Including pump casing, impeller, valve, etc. Castings can be cast in a variety of different alloy materials.
If you are in need of a pump now, you can contact us. We will provide you with the best solution. Email: [email protected]