Impeller damage causes and repair methods
The impeller is one of the key components of a centrifugal pump. Wear of the impeller is a frequent problem due to the frequent operation in harsh environments. Pump impeller wear can also have some serious consequences. For example:
- 1 The current and outlet pressure is unstable, causing the pump to swing violently;
- 2 The vibration of the pump increases. There are abnormal noises such as metal friction in the pump.
- 3. The axial movement of the pump increases. The temperature of the pump casing and bearing increases;
- 4 The flow at the pump outlet is reduced.
Severe wear on the pump impeller can cause the pump to not work properly. To ensure the maximum continuous operation time and operating efficiency of the pump.
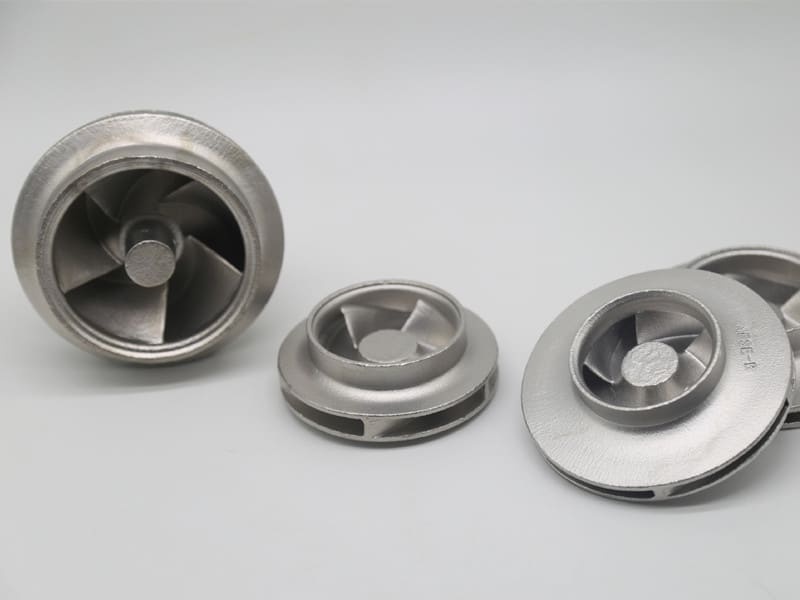
As a pump casting and pump impeller foundry, we cast pump components that account for 20% of our production. We also asked many customers and summarized some common impeller wear and impeller repair methods.
Common damage to the impeller
Several of the most common causes of damage to centrifugal pump impellers are cavitation, corrosion, erosion, and Fouling.
Cavitation
Cavitation is very dangerous for the impeller of any centrifugal pump. It is caused by the pressure difference on the pump body or the impeller.
When liquid is drawn into the pump, the partial pressure is lower than the saturation pressure of the liquid being pumped. Bubbles will appear at this point. Air bubbles implode as the liquid is transported from the suction side of the impeller to the output side. The implosion of the bubble creates a shock wave. This can cause damage to the impeller and other pump component surfaces.
When cavitation occurs repeatedly, it can cause pitting and fracture of the pump impeller and other components. Ultimately increases the flow resistance of the fluid being conveyed. Reduces pumping efficiency.
Problems caused by cavitation can affect the service life of the pump. In very extreme cases, it can reduce the life of the pump by about 10 years.
Corrosion
Corrosion is the result of a chemical reaction between the impeller of the pump and the liquid being conveyed. It is usually caused by the pH value of the liquid being transported being too low. When the impeller corrodes, it affects the efficiency and performance of the pump. Severe cases can cause pump failure. Failure to do so can increase the frequency of pump maintenance and downtime.
Selecting the appropriate casting material for the pump impeller can minimize corrosion. For example, cast iron can be used for pump housings. But if the pump impeller is made of cast iron material. And the transport of corrosive liquid will speed up the aging of the impeller. For corrosive liquids, a high-grade stainless steel cast pump impeller can be selected.
Besides to choosing the right material, there is also an option to coat the pump impeller with an anti-corrosion coating.
Erosion
The liquid delivered by the pump contains particles that wash off the surfaces of the pump impeller and other components. Over time, the surface of the impeller wears down and becomes very rough. This process is called erosion. If erosion is left untreated, it will eventually lead to severe wear on the pump’s interior. so that it cannot generate enough lift and may cause excessive vibration.
Erosion of the impeller is difficult to prevent completely. But, you can refer to the following two aspects to reduce the occurrence of erosion:
1- Decrease the flow rate of each section of the pump
2- Design the pump as a design with lower flow rates through tight running gaps
Fouling
Fouling is a common phenomenon, usually caused by the following conditions:
- 1- The particles contained in the liquid delivered by the pump can cause fouling.
- 2- If the pump is not used for a long time, it will also cause fouling.
- 3- Some liquids containing dissolved solids can also cause fouling phenomena.
Fouling of the pump impeller reduces the flow space for the conveyed liquid. Ultimately, the efficiency of the pump will be reduced.
Repair method of the pump impeller
During the operation of the pump, cavitation, corrosion and wear of the impeller are normal phenomena. Learning several impeller repair methods can repair damaged impellers in time. Common repair method: copper wire repair method (for copper impeller). Gas welding repair method. Quick steel repair method. Epoxy repair method. Surfacing repair method.
Copper wire repair method (for copper impeller)
The copper wire repair method is suitable for cavitation into a vacuum shape. And the holes are not connected into pieces. The specific operations are as follows:1. First remove the dirt and rust on the surface of the impeller blade. Can be applied to grinder operation;2. Use an oxygen-acetylene flame to blow out the debris in the pores.3. Fill the hole with copper wire of appropriate thickness. At the same time strike with a sharp hand hammer.4. Squeeze and squeeze the copper wire into the hole. Finally, smooth it out with a file.
Gas welding repair method
The specific operation of the gas welding repair method is as follows:
- 1- Heat the impeller to 300-500℃ with charcoal fire. And hang tin at the repair welding.
- 2- Fuse the brass wire into the hole that needs to be repaired.
- 3- Remove the charcoal after welding. Insulate the impeller by covering it with asbestos sheet to allow the blades to cool slowly. This prevents cracks from occurring.
- 4- After welding repair, use a file for processing and trimming.
Quick steel repair
Instant steel is a bonding repair agent. Has a strong adhesive effect. It is suitable for filling and repairing pores, cracks, sand holes, etc. of metal materials such as iron and steel. Instant steel is gooey before curing. After curing, it has high strength, high hardness and no shrinkage. The specific operation of the quick steel repair method is as follows:
- 1. First, clean up the floating rust and dirt around the repaired place. roughening.
- 2. Quickly and fully knead the colloid and outer skin materials in the quick-form steel plastic tube into one color. To achieve the effect of heat and softness. It takes about 1 to 2 minutes
- 3. Before the instant steel colloid solidifies, stick the colloid to the repair. And in the process of colloid curing, it is compacted many times. This can enhance the adhesion of the glue to the blade.
- 4. After the quick steel is hardened, fill it with a file.
Epoxy Repair Method
The specific operations of the epoxy resin repair method for the quick steel repair method are as follows:
- 1- Mix and mix epoxy resin, ethylenediamine, dibutyl phthalate, acetone, etc. in order and proportion.
- 2- Brush epoxy resin on the blisters and pores on the surface of the impeller blade. Try to brush evenly during the operation. And use a scraper to gently flatten and compact.
- 3- After the epoxy resin is cured for 1-2 hours, it needs to be brushed again 2 to 3 times. Make the surface of the impeller blade smooth and smooth during the last brushing.
- 4- After completing the above steps, place the impeller in a low relative humidity environment. The temperature is kept between 20 and 30°C.5 – After about 48 hours, the epoxy is complete. The impeller profile and surface are then trimmed.
Surfacing repair method
The specific operation of the surfacing repair method of the quick steel repair method is as follows:
- 1. In order to ensure that the surfacing layer and the impeller blade are combined more firmly. Before surfacing welding, it is necessary to clean the rust and debris on the surface of the impeller blade.
- 2. Preheat the impeller with a charcoal fire.
- 3. Overlay welding after preheating. In the process of surfacing welding, reciprocating welding or layered cross-pressure welding should be adopted. The amount of surfacing welding should be less each time. In this way, the heat concentration of the blade can be prevented, resulting in stress deformation.
- 4. Repair the impeller blades after repair welding.
The electrode of the surfacing repair method should be the same material as the blade. Or use a stainless steel electrode. After the impeller is repaired, a fine balancing experiment must be performed. This avoids the unbalance of the impeller due to the extra weight. Centrifugal force is generated during high-speed operation to cause the pump to vibrate.